Factory Culture of the Future: A sensible guide to Adhocracy
Imagine a fully synergistic organization, where silos are broken by common customer-centric objectives, a transparent flow of information and openly shared context.
EXECUTIVE SUMMARY
- Digitization necessitates a new breed of manufacturing leaders and employees
- To tackle this challenge, companies should slide towards an Adhocracy culture
- Adhocracy is, by definition, customer-centric, results-driven and innovative
- Cultural change trickles down, as each plant’s leadership leads by example
- For maximum effect, an orchestrated cultural transformation strategy is necessary
As the digitization of experience progresses inside and out of the workplace manufacturing companies face a monumental challenge: Establishing a culture that breeds a generation of lateral thinking leaders and workforce. The danger is twofold: First, high-performance today requires an entirely different skill set than the pre-Industry 4.0 era, which makes current leadership development methods insufficient. Second, for many executives, neglecting the development of human capital in favor of chasing the latest technological investment is tempting.
On the factory level, things get even more complicated. The need to take risks, innovate, and experiment has never been higher, but, at the same time, there is much greater transparency, which makes the cost of failure heavier to bear. Even though there’s a general top-down push towards out-of-the-box thinking and less rigid decision-making, most employees lack the skills required to manage the extra responsibility. Crucially, employees lack a suitable environment and culture to develop these skills in the first place.
To tackle this problem, manufacturing companies need to reconceptualize the way they approach their organizational culture, and embrace the concept of “Adhocracy”. Adhocracy, a term coined by American futurist Alvin Toffler, is an organizational structure specifically designed to accommodate a world of constant change. On an organizational culture level, Adhocracy is the antithesis of bureaucracy, and everything inflexible, old and sterile. It is the type of culture that nurtures intuition, decisiveness, and speed and welcomes diversity, innovation, and calculated risk.
The purpose of this article is to articulate the need for Adhocracy clearly – and give readers a straightforward guide they can leverage to drive change into their organizations.
Adhocracy Culture: Solve the problem; get the customer
Nowadays, business is not-as-usual. Whereas in the past the primary objective was to capture as much market share as possible, the primary objective has now shifted to creating more market. In other words: Innovation. There are three major reasons that explain this business shift towards innovation:
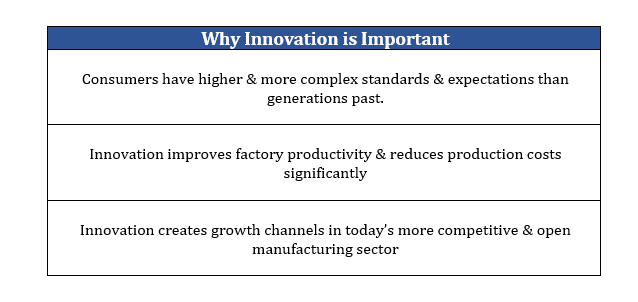
The factors above necessitate an agile workforce, that’s capable of managing uncertainty and fast-changing priorities effectively. To create this workforce, a dynamic, ad hoc approach to organizational culture is required. An Adhocracy culture, by definition, nurtures an environment where decisive and intuitive actions are encouraged and rewarded: Agile and fluid teams form rapidly to face urgent problems and challenges that conventional processes have failed to solve.
Whereas in a traditional system, the organization is organized around its set of rules, routines and business ethics, in an Adhocracy culture everything revolves around identifying and capitalizing on available opportunities. Externally-driven and results-oriented by definition, Adhocracy is characterized by a sense of urgency, a desire for continuous improvement, testing, and experimentation.
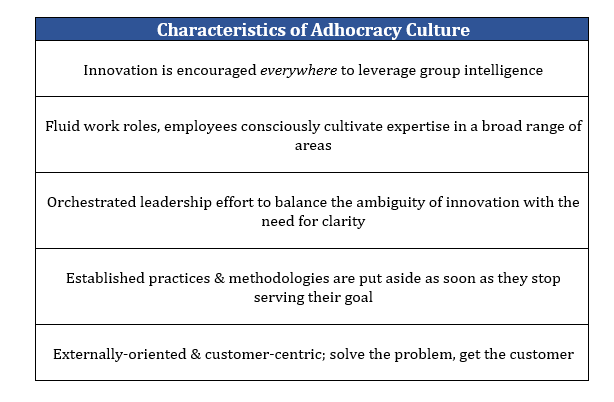
For most manufacturing companies, the value of establishing a culture of Adhocracy is clear: Greater responsiveness to customer and market demands, an empowered and more agile workforce, and the ideal environment to spark margin improving ideas. Consequently, the problem is not whether an Adhocracy culture is worth it. The real problem is how to get there when, up until now, factories have always been structured to be risk-averse, down to their core.
Sliding your organization’s culture towards Adhocracy
In SmarterChains’ experience, organic cultural change is too slow to keep up with the digitization of the manufacturing sector. Consequently, as a whole, companies need to rethink the way they incentivize and reward their employees to drive Adhocratic cultural shifts faster and more efficiently. This is an especially difficult task to accomplish, as Adhocracy contradicts the lean enterprise paradigm which is commonly encountered in manufacturing organizations.
For example, whereas Adhocracy encourages and rewards an explorational, experimentative approach, the lean paradigm is designed to eliminate all non-essential processes and therefore, leaves little room for risk-taking or error.
On the plant level, establishing the right conditions for Adhocracy falls to each plant’s leadership. To shoulder this daunting task, managers should first learn to operate in new ways on three different levels: Intellectually, emotionally and socially.
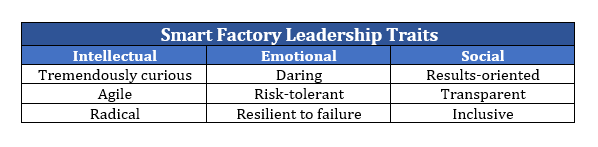
On an intellectual level, for instance, engineering managers must grow accustomed to having to make snap decisions about complex subjects without full visibility of all involved factors. On an emotional level, they must grow accustomed to high risk and develop a resilient “fail hard, fail often, fail forward” mentality. On the social level, they must be able to integrate diverse teams and establish common results-oriented patterns amongst cross-functional groups. As plant leaders shift towards a digital-ready mindset, the changes they experience start trickling down into the rest of the organization.
The next step is an orchestrated management effort to slide the entire organization towards an Adhocracy culture. According to Edgar H. Schein’s, “Organizational Culture and Leadership”, culture can be divided into three main areas:
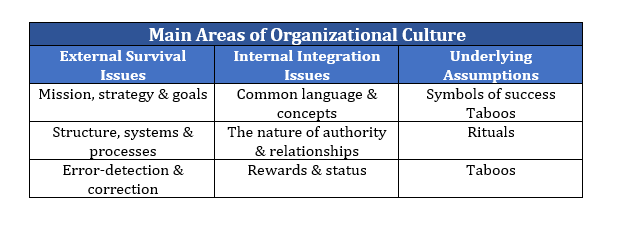
Using the table above as a starting point, manufacturing managers can begin mapping out their organization’s cultural change strategy. The transformation process starts with asking the right questions. For instance, the following table outlines a simple three-part question sequence, based on a “current stage, desired target, maintenance” model:
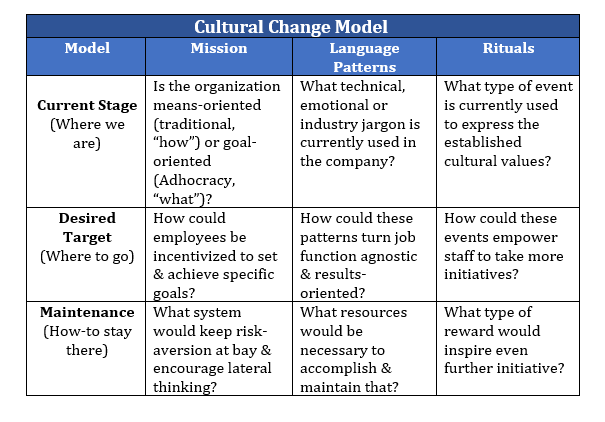
Naturally, after planning out the cultural transformation strategy, comes the execution part. Building up on our language patterns example, a possible solution would be to create or acquire a business glossary designed to break down communication barriers among different departments and distribute it among the workforce.
An excellent example and a great source of inspiration is eBusiness Institute’s glossary which is specifically created to address the siloed approach so common among companies older than thirty years old.
Next Steps
Imagine a fully synergistic organization, where silos are broken by common customer-centric objectives, a transparent flow of information and openly shared context. An organization where employees are personally invested in challenging existing systems and brainstorming new ways to improve margins, fixated on producing results, not passing their shift. An organization where the closest-to-action individuals are fully authorized and fully equipped to engage and solve the diverse problems they encounter in their jobs as they come.
This is the manufacturing company of the future.
The demands brought by the fourth industrial revolution, the extreme customer centricity pressure, and the ongoing need for continuous efficiency improvements necessitate this transformation. As natural cultural changes within companies are insufficient to keep up with present-day’s pace, forward-thinking manufacturing leaders should take a proactive stance and strategize on how to slide their organizations towards the culture of the future: Adhocracy.
In SmarterChains’ opinion, a holistic organizational shift is a strict prerequisite for continued margin improvement and Industry 4.0 expertise as the world ventures forth into an increasingly complex age. In this, establishing an Adhocracy culture across factories is perhaps the most important transformation enabler.